Achieving high precision and fabrication results are essential in the world of manufacturing, with many sectors requiring quality components that are often complex and intricate. Two important standout techniques have emerged in the modern era, providing detailed and rapid solutions that retain quality. They are also known as laser cutting and CNC milling, each performing similar tasks in their unique way. This guide helps businesses understand the difference between each process, helping guide the path towards the most suitable technology for their project.
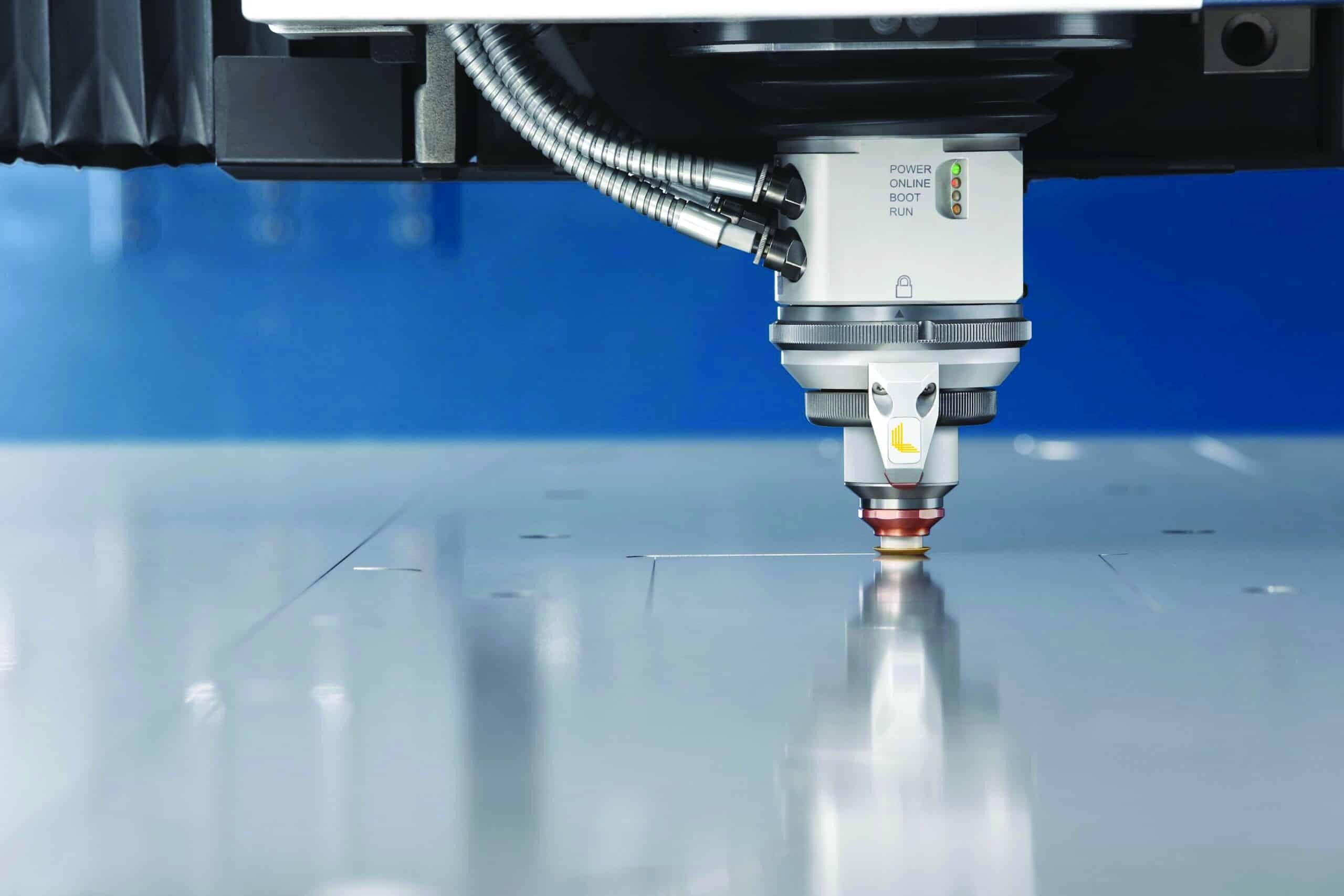
What is Laser Cutting?
Laser cutting utilises a concentrated high-powered laser beam that generates controlled heat to vaporise, melt or burn through material, achieving a clean-cut and incredibly precise edge. The most common methods of laser cutting are fibre and CO2 lasers, both offering thermal processes that can create complex shapes and detailed designs, regardless of project scale and often without the need for post-processing.
Laser cutting is a non-contact process, so there’s typically no risk of contamination or damage to the material structure, protecting its integrity. Operated by CAD technology, the laser follows a path that ensures it outputs the same level of quality across a variety of materials including metal, wood, acrylic, textiles, plastics and more. Although material thicknesses are a consideration during the process, with the advancement of new technology, this is not so much of a concern.
What is CNC Milling?
CNC milling, also known as Computer Numerical Control, is a precise process that removes material through a rotating cutting tool to achieve a desired shape or design. This method of machining follows a guided path set by parameters as defined by computer instructions, ensuring the machine achieves consistent results across large volumes of production.
Unlike laser cutting, CNC machining uses a contact process which involves various tools to drill, grind and bore material, which may often require post-processing solutions in order to eliminate sharp edges or imperfections. Despite this, CNC milling can be used on a variety of materials including metals, plastic, wood and composites within small tolerances, making it a valuable resource across a magnitude of industries.
In addition to standard laser cutting and CNC milling, laser bevel cutting has emerged with innovative technology to cut 50° bevels and countersinks to any size, automating and producing fabrication ready parts that eliminate the need for additional weld preparation. Building upon the existing advantages, bevel cutting introduces precise cutting angles in a single step, stepping away from additional processing and mechanical grinding.
The Differences in Metal Profiling Applications
Cutting Method
The primary difference between laser cutting and CNC milling would be the way they cut materials. While laser cutting is a contact-free process, CNC machines are not, which often requires the need for additional post-processing such as deburring or shot blasting to eliminate imperfections.
CNC milling can also be more intricate in its capabilities, particularly due to its ability to produce three-dimensional shapes, which is ideal for sectors that require complex geometric shapes. On the other hand, laser cutting stands out when it comes to producing clean, intricate and precise cuts in rapid lead times. With further technological advancements in laser cutting, it has become exceptional at maintaining material integrity from thermal damage, minimising the heat-affected zone and potential distortion.
Material Capacity
Both laser cutting and CNC milling can accommodate a broad spectrum of materials, with small differences between them. Generally, CNC machining can process most hard and soft materials such as alloys, metals, composites, wood and plastics, which provides scope for versatility.
Laser cutting can cut the same materials, and is especially exceptional on thinner materials such as steel, aluminium and brass. In the past, laser cutting machines have faced difficulty cutting thicker or reflective material, which has been showcased mostly on CO2 lasers. Fibre laser technology addresses the previous challenges with ease, offering industries further opportunities to achieve their desired results.
Where bevelled cuts are required on materials up to 40mm thick, laser bevel cutting provides an efficient alternative to traditional methods, allowing for greater control over geometries and quality.
Precision and Tolerances
Both processes are known for their highly precise capabilities, with CNC milling slightly taking the edge. Depending on the design and material, CNC machining can achieve tolerances within ±0.13 mm, which is essential for mechanical and detailed components. Likewise, laser cutting performs incredibly well to a tolerance within ±0.025 mm, especially on thinner materials. However, depending on the design, desired finish and material depth, laser cutting can outperform CNC milling for very fine and complex requirements.
Laser bevel cutting retains high precision while adding the flexibility of creating angled cuts within tight tolerances. This is particularly beneficial for components that require highly precise weld fits and seamless chamfers.
Speed and Efficiency
Laser cutting is renowned for its remarkable lead times, processing large-scale projects in rapid succession. The laser beam moves quickly, and due to its non-contact ability, it can reduce wear and tear on the machine and speed up the process. This is particularly beneficial where precise quality components are required for high throughput projects.
CNC milling is generally slower than laser cutting, especially when it comes to processing complex shapes. This is due to the additional contact required during manufacturing, which will also impact the lifespan of the machine.
Laser bevel cutting further increases efficiency by eliminating the need for separate bevel stages, delivering fabrication ready parts in rapid lead times and enhancing downstream efficiency. This is ideal for sectors working within tight deadlines.
Cost Considerations
Over time, CNC milling machines can be more expensive to run and maintain, particularly for multi-axis models. Since the tools will wear out over the years, they will need to be replaced, which adds to maintenance expenses. This can be reflected in the cost of projects, especially if additional finishing is required.
Laser cutting has a lower initial investment, far less maintenance requirements and the additional benefit of speed. Although this can vary depending on material type and depth, laser cutting is often very cost-effective for sectors with large projects or complex designs.
With laser bevel cutting, cost savings are further enhanced by reducing the number of processing steps required for edge preparation, making bevel cutting an ideal solution for both one-off and large-scale projects.
Applications of Laser Cutting and CNC Milling
Both CNC milling and laser cutting have a lot of crossover when it comes to the sectors they can provide services for, the main ones including:
- Aerospace
- Automotive
- Medical
- Electronics
- Construction
- Architectural
- Jewellery
In most cases, CNC milling is found to be used in complex shape production such as gears, brackets and engine components. Laser cutting offers various potential for cutting and engraving, and is used widely across many manufacturing requirements.
Alternatively, laser bevel cutting is particularly advantageous where angled or weld-prepped components are required, offering a high degree of accuracy and consistency across batches without extensive additional labour costs.
The Alternative to Laser Cutting and CNC Milling
Laser bevelling is an exceptional alternative to laser cutting and CNC machining for bevelling edges up to 50°, offering faster and more efficient processing times while still being more cost-effective due to its streamlined processes.
Laser bevel cutting can accommodate complex bevel geometries on materials up to 40mm thick, reducing margins of error for small and large-volume projects. This method eliminates unnecessary steps and procedures, providing fabrication-ready and weld prepped parts with greater efficiency.
The Laser Cutting Co. – Your Expert in Quality Laser Cutting Services
With over 40 years of experience, Laser Cutting Co. have a depth of knowledge across a magnitude of industries and fabrication requirements. Our expert engineers encompass laser cutting, bending, welding, laser bevel and sub-assembly services, all under one roof.
We’re committed to delivering the utmost quality, which is why we integrate smart design production through CAD software for maximum and streamlined efficiency, producing outstanding results.
For tailored requirements and further guidance for your business, contact a member of our team today.